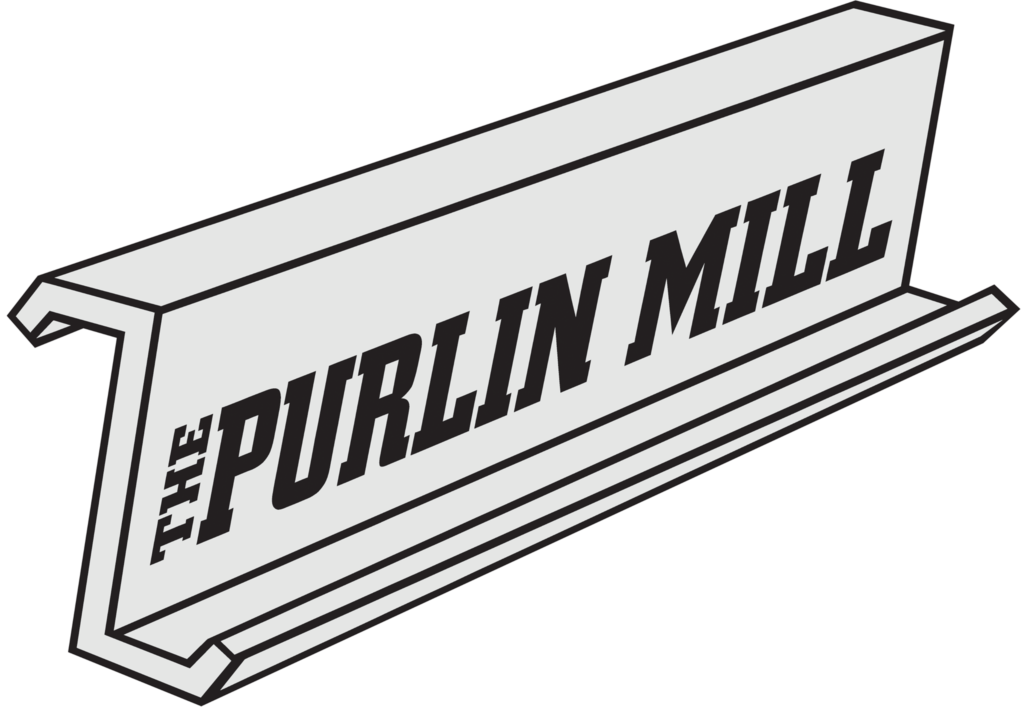
GALVANIZED PURLINS AND GIRTS
GALVANIZED COATING
Our steel coil is hot dipped galvanized to protect the bare steel from corrosion and provide maintenance free longevity of our products.
Not all galvanized is the same. There are different designations of galvanized steel-based on the ounces of zinc per square foot of both sides of steel. (G-40 Galv.) For example: Translates to .40 oz. of zinc, .20 oz. on the top of the steel, .20 oz. on the bottom in 1 square foot.
Many of our competitors use a relatively low galvanized coating. The higher the coating weight, the better your steel is protected from rust and corrosion. The higher the coating weight, the longer you are protecting your investment.
The Purlin Mill uses G-90 Galvanized Steel .45 oz. of zinc are used on each side of the steel per 1 square foot. (.90 oz per square foot.)
Made specific for the Pacific Northwest Environment, a beautiful part of our country. We have sun, lots of rain, a wet damp atmosphere for many months, snow and even more environmental conditions for steel corrosion along our wet coastal range.
Hot dipped galvanized sheet steel provides a uniform zinc coating protection over the bare steel. This process is the most effective corrosion protection system available to our customers. Making our products more durable and maintenance free for decades.
Zinc used in the galvanized process and our steel is 100% recyclable materials.
COATING THICKNESS
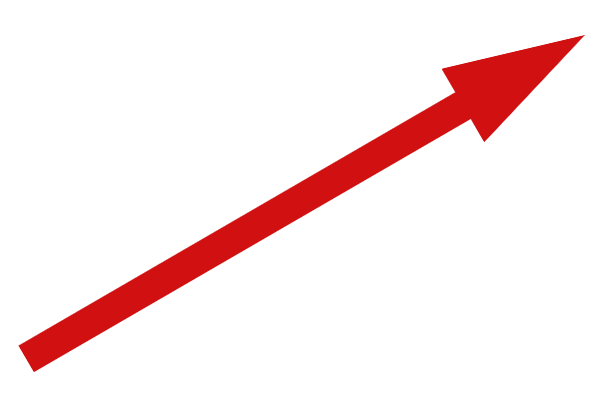
OZ OF ZINC
.40oz
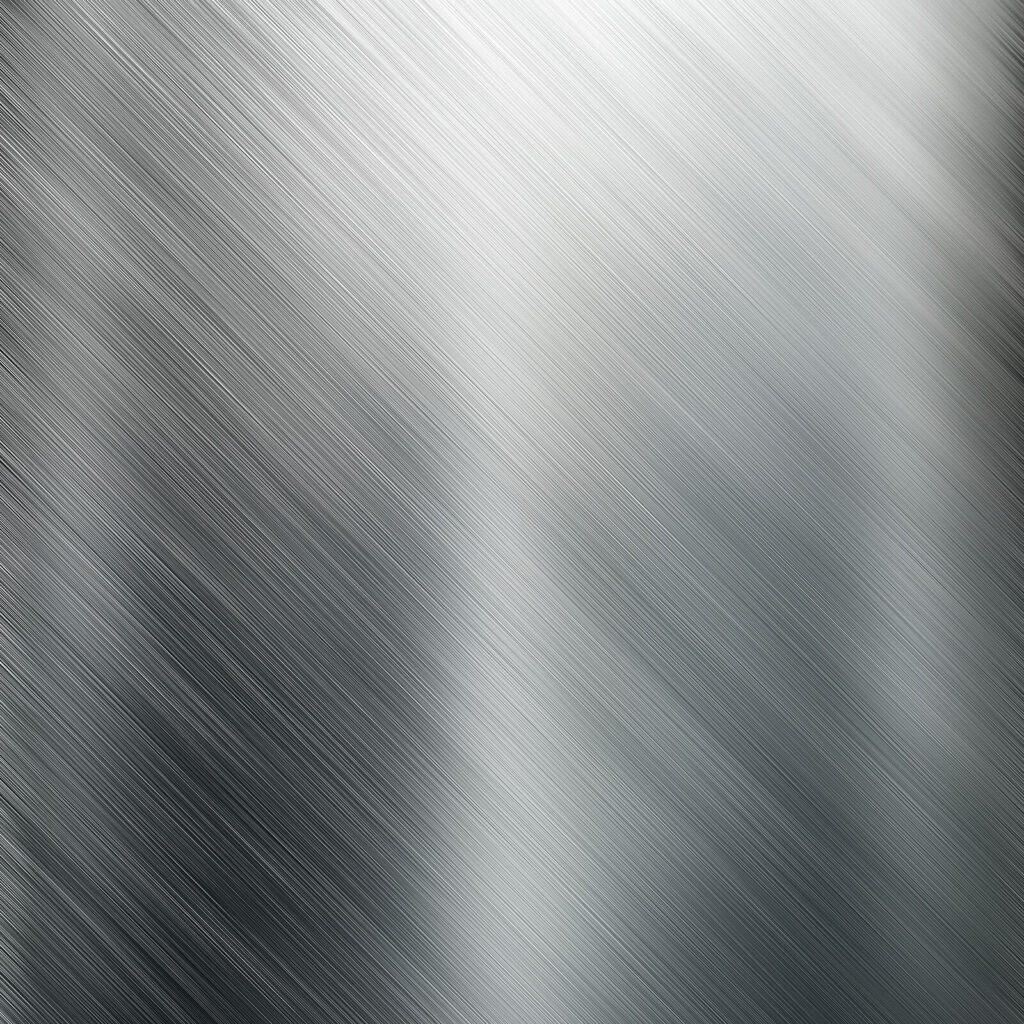
G40
OZ OF ZINC
.60oz
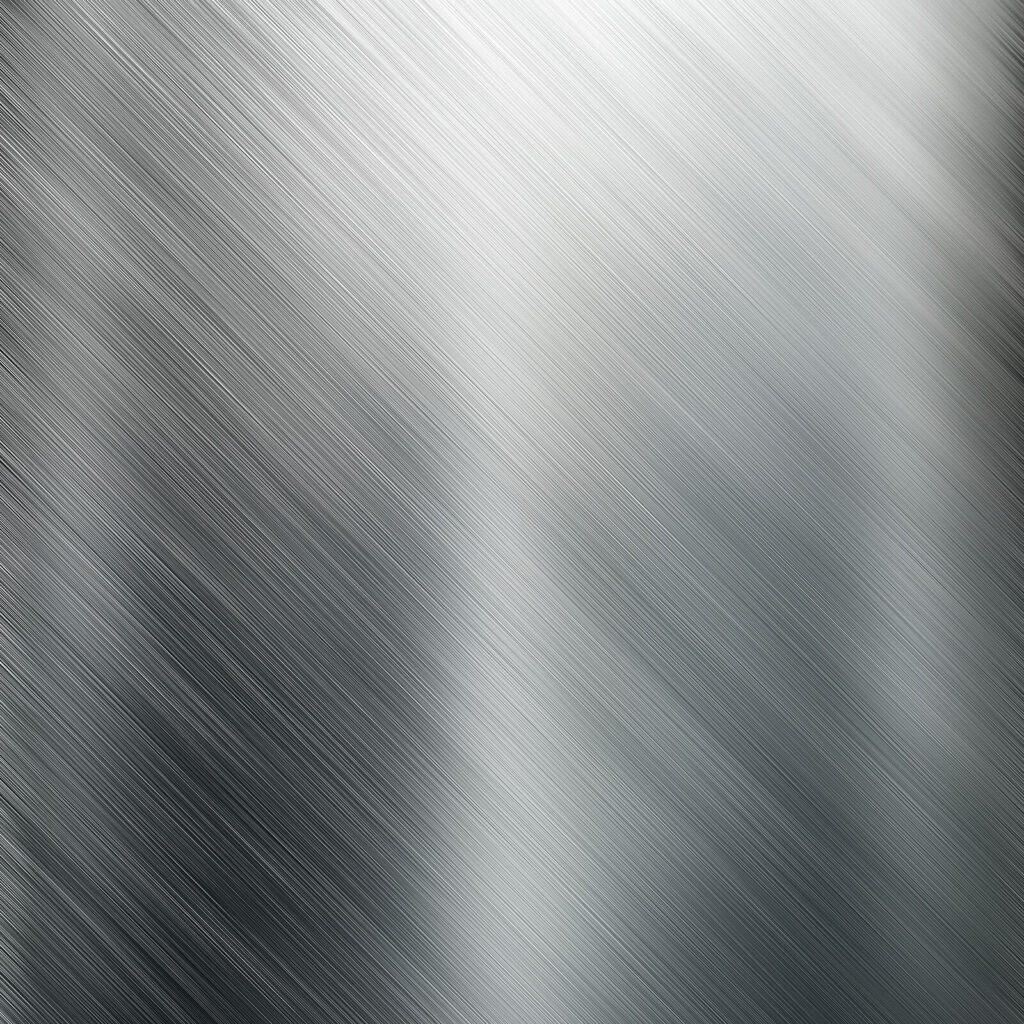
G60
OZ OF ZINC
.90oz
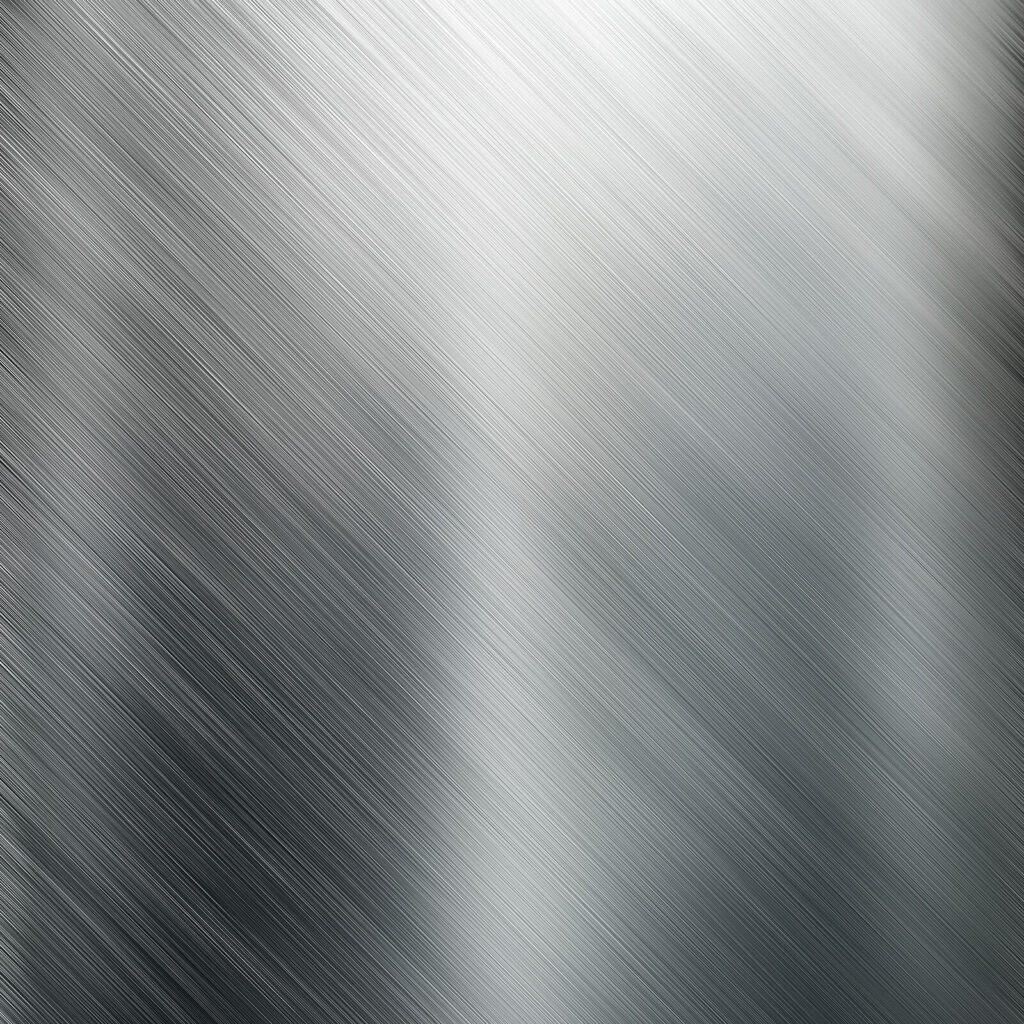
G90
OUR PROTECTIVE COATING
Typically, the greatest threat to a steel framed building is moisture. If your bare steel is not coated with the correct protective coating, moisture damage will cause rust and corrosion which will eventually compromise a buildings integrity for which it was designed. Galvanization or Galvanizing is the process of applying a protective zinc coating to steel or iron to prevent rust and corrosion. The Purlin Mill’s steel is hot dipped galvanized, in which our coil is submerged in a bath of molten zinc. Once it cools, the steel and zinc are tightly bonded creating a tough protective coating that will last 50 years in most rural environments.
Zinc coating weight thickness is measured in ounces per square foot (oz/ft²). The coating weight should be carefully chosen with extra attention to the type of environment in which the finished product will be expected to serve. Generally, the effectiveness of the zinc coating to protect the steel substrate from corrosion in any given environment is directly proportional to the zinc coating thickness. ASTM International designates zinc coating weight standards such as G30, G40, G60 and G90. A designation of G30 is, galvanized with a two-sided zinc coating weight of .30 ounces per square ft (oz/ft²). G40 is, galvanized with a two-sided coating weight of .40 ounces per square ft (oz/ft²).
A G90 galvanized coating will last about 50% longer than a G60 coating, maintenance, painting and all other factors being equal. The Purlin Mill recognizes that our Pacific Northwest environment can be more corrosive to steel than other regions of our great country. We have witnessed steel buildings where moisture in the purlin cavity caused enough corrosion to deteriorate the purlins, compromising the design loads of the building. The purlins and roofing required replacement. It was an unexpected costly surprise to the building’s owner. This is why The Purlin Mill uses G90 galvanized steel on all of our structural products. We don’t always know the environment that our product is being exposed in. Why take chances? The Purlin Mill doesn’t. Our G90 galvanized steel provides long-term corrosion protection. It’s made specifically to withstand the corrosive elements of the Pacific Northwest.